
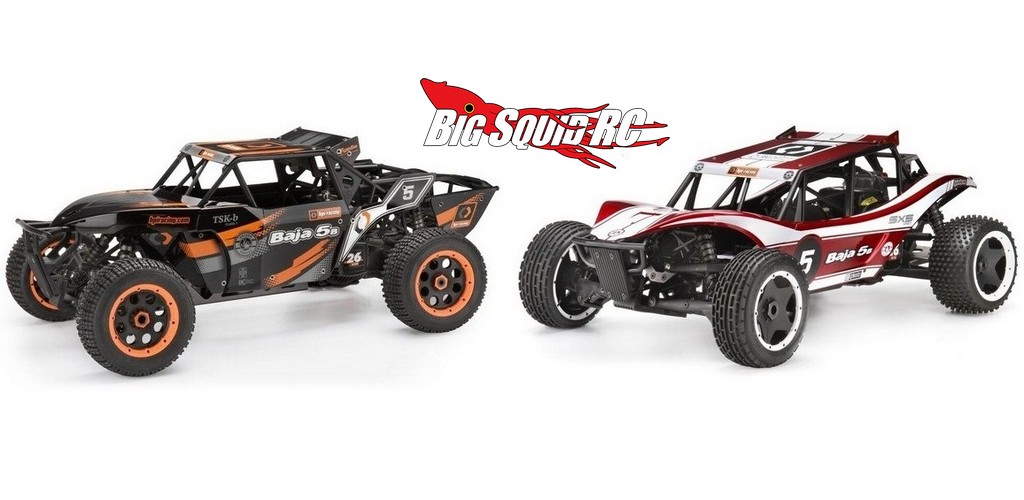
* Each Flux} window will onComplete once it contains maxSize} elements * OR it has been open for the given Duration} (as measured on the Schedulers#parallel() parallel} * Scheduler).
#Flux window windows
And you’re done./** * Split this Flux} sequence into multiple Flux} windows containing * maxSize} elements (or less for the final window) and starting from the first item. Rinse with water and buff dry with a rag. Re-apply as needed to get all the zinc and lead uniformly black. 3 hours ago &0183 &32 The first transfer portal window since the concept became official last fall closed on Thursday morning, marking the end of the 60-day period where first-time transfers could put their name in the. This is achieved by brushing on black patina liquid. So this is when you use “whiting compound”, calcium carbonate powder to clean the glass and remove excess putty.Īt this point the lead is a shiny silver color. The putty will have made a smeary mess on the glass.

Turn it all over and squish putty into the other side. It’s messy and I use my fingers to push the putty in. This is simply squishing window glazing (putty) into all the voids between glass and lead came. Then I move the plywood to the other side to ease it down.Īfter all zinc and lead joints are soldered and look good, it’s time to glaze. The panel is pretty fragile at this point so I slide a piece of plywood under it to lift it to vertical. After all joints are soldered, turn the whole thing over and solder joints and the other side. Brush some flux onto a few joints, the solder the came together.

This wouldn’t be necessary if the zinc border were left “open”. To fit the final pieces inside the zinc boundary, it was necessary to partially lift previously assembled pieces to provide some space for the final pieces to fit in. I try to get the lead came pieces to fit snugly together so they’ll solder neatly later. Why horseshoe nails? They’re a convenient size, and their wedge shape tends to press in on the lead came as you pound the nail into the support board. I then started at the left side, cutting and fitting, and holding the partial assemblies together with horseshoe nails. That way I was guaranteed that I’d end up with the required size. I started by cutting the zinc edging to size and soldering it together. This usually makes a stronger result, and it looked more appropriate for the size of pieces in my design. The other method uses pre-formed H shaped strips of lead, called “came” between the pieces. There are two popular types of stained glass: There is Tiffany style, where each piece of glass is edge-wrapped with copper foil, assembled like a jig saw puzzle, then soldered together. Grind down rough edges or too-large parts until the part fits neatly within the lines on the cartoon. It’s possible to adjust the edges by crunching the glass edge with pliers. The bumpy side is more interesting, and that will be the “front” or more visible side of the final panel.Ī glass grinder is essential. I try to keep smooth sides up when fitting to the pattern. It’s easier to cut the scratch on the smooth side and do the whacking on the bumpy side. Sometimes there will be undesired breakage.įor straight cuts, I lay the larger side on a table, scratch positioned over the table edge, then use a glove to grab the smaller side and force it down until it breaks.Ĭolored glass often has a smooth side and a textured or bumpy side.
#Flux window crack
Some types of glass crack easily and predictably, and some take a lot of hard whacking.
#Flux window trial
Trial and error determine how hard you need to whack. If you’re lucky, a crack will start to form at the scratch, and the crack will grow along the scratch as you continue to whack the glass. You’ll have to make a paper cut-out (template) of the piece and trace onto the glass.Īfter there is a definitive scratch on the glass, I use the steel ball end of the glass cutter to “whack” the glass behind the scratch on the other (non-scratched side). Troubleshooting: Flickering and Tinted screens f.lux doesn't work on Windows 10. Most people can find find advice here that will make v4 better for their needs. Note that if the glass is opaque or too dark, you can’t see through it to cut. We do not recommend using v3, as it has signficantly more performance impact on the system.
#Flux window free
But for curved lines it’s free hand and it’s easy to stray from the lines. This is easy for the straight lines and I use a ruler to keep them straight. The scratch is where the glass will crack and separate. The way I try do it is to lay the glass on the design, use a strong light to look through to see the lines, and run the cutter along the lines, making a visible scratch the entire way.
